Equipment
Instrumentation Park for the Laboratory
Gallery Overview
- Digital and analog oscilloscopes. 100 mHz Bw
- Digital 6 ½ digit precision ultimeters. 300 kHz Bw
- Power supply 0-30 V 3A
- Digital multimeter 3 ½ digit handheld multimeter
- Power bench for component testing
- Durability bench for braking material testing
- Custom intrumentation for testing

Class 100,000 Clean Room
The company’s laboratory is equipped with a class 100,000 Clean Room on about 40sq.m. with five work stations and controlled temperature and humidity. All the work carried out inside are dedicated to the production of mechanical and electronic assemblies that are used mainly in the military, avionics and space sectors.
With the introduction of the class 100 horizontal laminar flow tables, particular attention has been given to optical assembly.

Climate Room
The company's laboratory is equipped with a Climate Room to simulate the most diverse climatic conditions, which makes it possible to carry out temperatures tests in the -55 °C and +155 °C range and humidity tests in the 10% and 98% range.

LT 400 system
The company’s laboratory is equipped with a LT 400 system designed to perform Partial Discharge Measurements on components and Surge, for improving the quality of production processes of any type of motor or winding. Partial Discharge tests are performed according to the
IEC EN 60034-18-41 Technical Specificatons. They make it possible to identify motors that, although functioning, can present problems after working for a short period, in particular if they are powered by INVERTER.
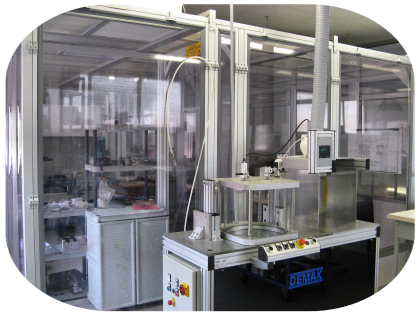
Vacuum Chamber for resin potting
The company’s laboratory is equipped with a Vacuum Chamber for resin potting. Potting under vacuum is frequently required to prevent air entrapment, especially with the increasingly small and complex assemblies required in today's electronics. The potting of electronic components involves filling the assembly with a compound, such as liquid resin, to protect it from environmental conditions or when using it in conditions of moisture, humidity, and vibration. Any air entrapment in the potting compound can result in air bubbles that may cause performance problems in the finished component. This system provides a proven solution for maintaining a dispensing environment which is free from air.